We can provide the most suitable oxidizer, depend on characteristic features of dryer, because we also design and manufacture dryer by ourselves.
The systems of thermal oxidizer correspond to changes of exhaust gas volume, solvent concentration and operating conditions of the production machines.
Direct flame type thermal oxidizer
It can easily treat the exhaust gases with little influence by the substance in the exhaust gases, and can keep high rate of the oxidization effect in the long life operation. However, it is said that the running cost of direct flame oxidizer is generally high. So we propose the combined system with hot air recovery system by gas-gas heat exchanger and heat recovery system by waste heat boiler (steam type or thermal oil type).
Catalytic type thermal oxidizer
Generally, it uses gas or kerosene as fuel. But depending on the solvent concentration conditions, it can be operated by self-combustion with catalysis only.
In addition, although there is a case that the catalytic function is declined by silicon and metal vapor, it can keep its life longer by using pretreatment (Guard Bed) or Catalyst Rejuvenation.
In this system, the waste heat is recovered as hot water and hot air, or usually re-used as the heat source of the dryer.
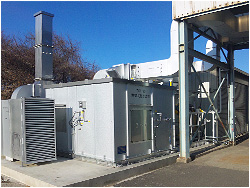
We had developed of economical type catalytic oxidizer using poisoning resistance catalyst and we installed the system in operation for dry laminating machine.
This system adapts “NHP” as poisoning resistance catalyst developed by Nikki- Universal Co., Ltd. who is famous as high quality catalyst supplier. By using “NHP”, the estimated life time of the catalyst becomes 3 or 4 times longer than ordinal one, and the reaction efficiency for ethyl-acetate-containing exhaust gas is improved remarkably with the low temperature in the range of 250 ~ 300℃.
In addition, we propose energy saving system recovering the surplus waste heat to use as heat source for the dryer, and system for CO2 emission treatment.
Regenerative thermal oxidizer (RTO)
The temperature required for this system is 800 ~ 900℃ , which is higher than direct flame type. But by using suitable regenerative media, the running cost can be reduced toward the level of one tenth or twentieth of the running cost of direct flame type. In addition, it can be operated by self-combustion at 500ppm of toluene base. In the case of high concentrated exhaust gas, steam recovery also is possible.
Thermal oxidizer combined with VOC concentrator
In this way, the exhaust gas highly concentrated about 10 times is treated with smaller oxidizer. At the same time, the recovered high temperature exhaust gas is re-used as the hot air for the solvent removal and adsorption.
Recently, considering the additional installation of the printing press in future, the idea to install one 500Nm3/min scale oxidizer connected with common exhaust gas header from printing presses was adopted with the controlling the number of oxidizer system according to the operating condition of the printing press.
This system makes it possible to minimize the running cost of oxidizer and can add the oxidizer step by step according to the number of the printing presses.
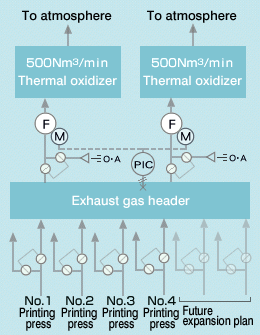